In-mold electronics (IME) combines in-mold decoration (IMD) with printed electronics technology. According to the structure, first IMD inks, then conductive, thermoformable inks, and finally IMD inks are printed with the screen-printing process in 2D to thermoformable substrates, such as polycarbonate films. These printed films are then thermoformed and finally back-injection molded, for example with polycarbonate.
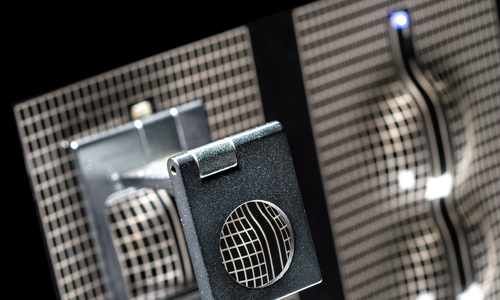
The complex multilayer structure of IMD and conductive inks poses certain challenges. On the one hand, it can result in the fundamental incompatibility of the ink systems with each other and, on the other hand, it is necessary to ensure that the individual layers dry completely. During the printing process, it may already be possible to observe the incompatibility of the systems with each other, for example in the form of poor wetting. It can also occur that the incompatibility can only be recognized after drying and measuring the resistance of the conductive ink.
In our application technology laboratory, we tested different structures with IMD inks of the common manufacturers together with our Bectron® CP 6680 and Bectron® CP 6681 conductive silver inks.
In addition to the good preparation of the inks before printing, such as adaptation to room temperature and through stirring, we recommend the following printing and drying procedure:
- Printing the IMD ink x times to the required substrate, for example a polycarbonate film. The number of printed layers x depends upon how intense the colouring should be. For a dark, intensive black, at least 5 printed layers are recommended.
Each printed layer must be dried at least 5 minutes at 80°C. Before printing the conductive silver ink, dry 30 minutes at 80°C and wait at least 24 hours before proceeding further. - Printing the Bectron® CP 6680 or Bectron® CP 6681 conductive silver ink with a 71 - 100 1/cm stainless steel or 71 - 90 1/cm polyester screen over the IMD ink and drying for 10 minutes at 120°C.
- Printing the IMD ink x times over the conductive silver ink and the lowermost IMD ink layer. Once again, the number of printed layers x depends upon how intensive the colouring should be.
Each printed layer must be dried at least 5 minutes at 80°C and the final drying step requires 2-3 hours at 80°C before the back-injection moulding of the films in the next step. - According to the IMD ink manufacturer, some recommend the use of an adhesion agent as the final layer before back-injection moulding.
The diagram below illustrates the behaviour of the resistance for the Bectron® CP 6680 conductive silver ink during this printing process:
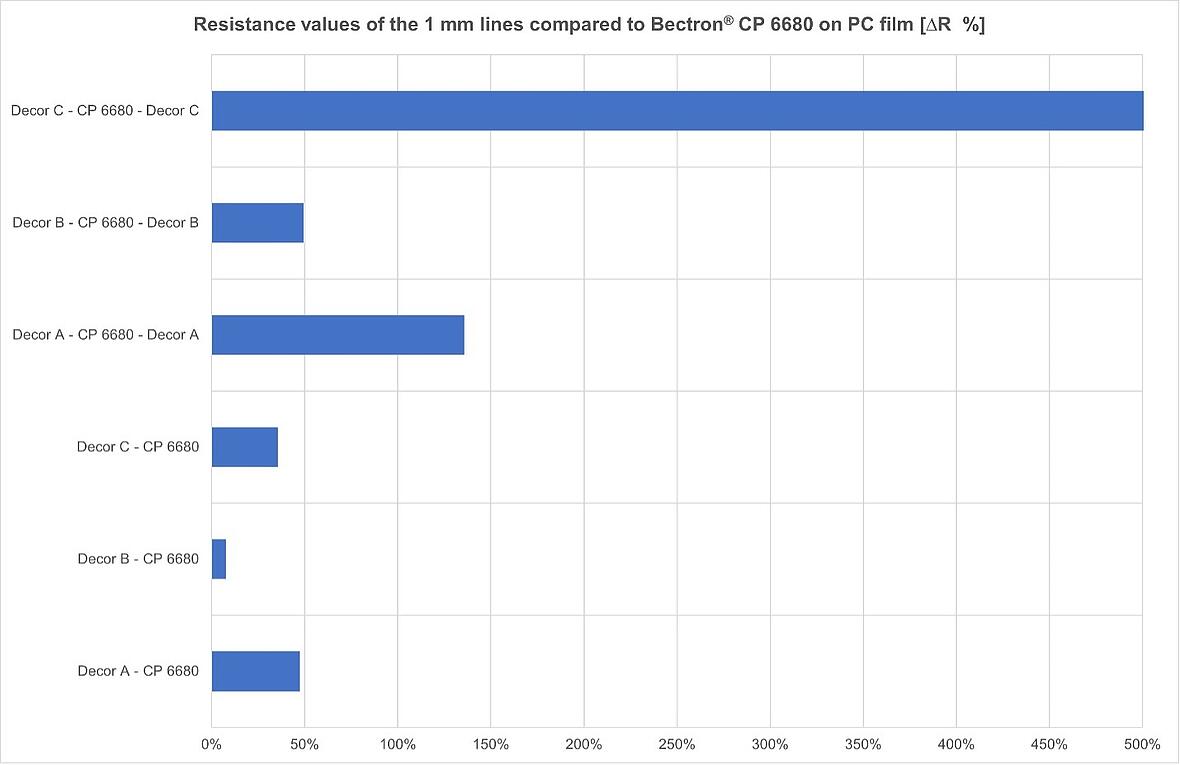
The diagram compares the change in the resistance of Bectron® CP 6680 with the resistance of Bectron® CP 6680 printed to a polycarbonate film and Bectron® CP 6680 printed between the IMD inks.
The change in the resistance for printing the Bectron® CP 6680 over the IMD inks A, B and C was between 8 and 47%. When the IMD inks were printed again over Bectron® CP 6680, this resulted in a change of 49 to more than 500% for the resistance.
The results clearly show that not every combination of IMD and conductive ink is suitable. Based on our experience, we can offer initial recommendations for technical implementation and of course also support you with your projects.
You’ll find additional information on the products described under the link below. There and in our technical datasheets you can also find relevant recommendations for other insulating and conductive screen-printing pastes: https://www.elantas.de/europe/products/printed-electronics/products.html
We will be pleased to answer your questions directly and offer suitable products in support of the technical implementation of your products. Simply send us an e-mail: AdvancedPrinting@ altana. com