Join us at our 5th Printed Electronics Days Conference where industry experts will share their knowledge on cutting-edge and specialized topics from various angles and first-hand. With a lineup of 18 engaging lectures, you'll explore the entire process chain, from functional inks and printing techniques to market insights and best practice applications. A special focus will be on innovation and trends.
Registration fee € 320,00 excl. VAT per person
Venue: Hotel Hafen Hamburg, Seewartenstr. 9, 20459 Hamburg, Germany
In this presentation you will have an insight of ALTANA and ELANTAS latest information, including the acquisition and integration of Von Roll; within this frame you will hear how the Printed Electronic product group, belonging to the ELANTAS division, can benefit by the competences of a strong technical specialty chemicals company like ALTANA.
Thin, light, flexible and robust are the key characteristics of printed electronics, which can be seamlessly integrated into a wide range of products. This enables new applications in a variety of industries, including automotive, consumer electronics, healthcare, printing/packaging and smart buildings, as well as its growing presence in the Internet of Things (IoT) - in short, "electronics everywhere". At the same time, there is a growing need for sustainable and circular electronics due to its quantities but also specifics of conventional electronics. Flexible and printed electronics enable more sustainable electronics by using new materials and processes, as well as through their lightweight nature.
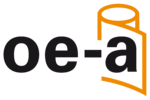
Dr. Klaus Hecker
Managing Director
OE-A (Organic and Printed Electronics Association)
A working group within VDMA
The presentation will give an overview of current and latest activities of Fraunhofer IZM in the field of flexible, stretchable and conformable electronics. The focus is set on key technologies which are based on established printed circuit board, thermoforming and molding processes, which, through combination and adaption, lead to completely new, hybrid manufacturing concepts with high potential for innovative products and applications. Based upon current project results, challenging topics, such as additive vs. subtractive patterning, overall process compatibility and interconnection are picked out and discussed.
With the growing trend of surface functionalization, digitalization, and further need for data generation, printed electronics and, in particular, wearable technologies are rapidly entering different markets. For the realization of lightweight, thin, and above all, flexible solutions, the use of film-based systems is advantageous. Due to the specific requirements of printed electronics applications, special films need to be developed which are tailored to the needs of each application. One group of materials that can be tailored in a broad range and meet these requirements are films made from thermoplastic polyurethane (TPU). Especially for use as a substrate for printing sensor systems, TPU films show promising properties.
Two main advantages of Printed Electronics are flexibility and transparency. Both features complement traditional electronic systems. At Kundisch we devote our production and development efforts to these advantages. In this presentation we will show the latest advances in transparent antennas and their production with high yields. The challenge of high conductivity, freedom of design and high transparency is mastered in these products.
Additionally we show how to integrate ICs in stretchable products converting analog signals to digital as near to the signal source as possible. A possible game changer wearable electronics where contacting has been a real troublemaker in the past.
There is a new star on the printed electronics firmament: FLEXOO. What is FLEXOO? FLEXOO is a new company with a long history. If you want to lean more, my talk is the right place. I will explain where FLEXOO comes from, what our specialties are, and most importantly, what we are doing. This comprises our engineering and development capabilities, our production knowhow, and the advantages of our special equipment. All this explains our infinite possibilities.
Finally, I will provide several case studies with our industry customers and explain the connection between FLEXOO and the Mars. Believe it or not, NASA is involved. And no, I will not talk about solderable copper ink.
Functional inks applied on flexible substrates is one key application in the scope of “Printed Electronics”. Creating electronics may require mounting of functional components such as LEDs, sensors, or ICs. PET is very often used as such a flexible substrate making low temperature processes mandatory.
To keep the functionality and the flexibility of the printed and mounted substrate, additional stabilization of the components might become necessary. The presentation shall provide some ideas and solutions how to cope with these challenges.
Witte Technology has used printed electronics to achieve a milestone in the digitalisation of care and successfully put a sensor for digital incontinence management into series production.
This sensor can reliably monitor the urine fill level and .
Monitoring the urine fill level of the incontinence products- Movement monitoring- Pressure ulcer prevention- fall detection- Zone management for dementia patients. In addition to the reliable performance of the sensors, a key challenge in the development of this medical product was the price and scalability of the solution. Printed electronics offer clear advantages here compared to conventional electronic component designs
The demand for printed electronics, especially sensors, is constantly growing over the last few years. Standard printing techniques like screen or inkjet printing are widely used with great success. Most of the substrates are two dimensional like foils printed in a either roll to roll or sheet to sheet process.
Often these substrates have to be connected with the actual surface where the function is needed
for instance via an extra gluing or laminating process. In contrast, the binder innovation and technology center is using an alternative approach. For three dimensional or structured substrates, pad printing is used. The function is directly printed on the substrate without any additional process. During the printing process, the paste is transferred from a printing form (cliché) via a silicon pad directly on the substrate. This process is well established for high volume production in marketing or graphic printing.
In order to achieve a reproducible and stable functional layer special needs of the printing pastes in terms of viscosity and homogenous preparation are required. Typical line widths are 80 - 100 µm and a layer thickness of 8-15 µm. Applications range from force and touch sensors as well as heating devices or bioelectrodes.
Although not intended for this printing technique binder uses different ELANTAS printing pastes for this purpose with great success since many years.
New applications in the field of printed electronics require higher demands on the functional pastes used and pose new challenges for further development. In this presentation, the current topics in research and development at ELANTAS Europe GmbH will be presented.
One focus will be on the development of paste combinations for printing fine structures (including multilayer structures) on a wide variety of substrates. The future reduction of silver with the possible use of copper also has an influence here. On the other hand, the demands on the insulators used as a migration barrier are increasing. Accordingly, part of the development is the further optimization of the screen-printable insulators used, also with regard to transferring methods from conventional electronics to printed electronics.
When it comes to Printed Electronics in industrial products, no customer will pay more for a product, just because it contains features based on Printed Electronics or you show him a fancy demonstrator. Come and find out about “Digital Elastomers” - The transformation of industrial rubber products into digital systems.
Silver based conductive ink is the backbone of the Printed Electronics. Unfortunately, silver metal price is almost doubled in the last five years. Therefore, there is an urgent need to find a low-cost alternative. Saralon offers a low-cost copper-based conductive ink with comparable conductivity. Different applications based on Saralon’s copper ink will be explained during the presentation.
In this presentation I want to take you through the process of a print test in our Customer Experience Center. We will use a recent case together with Joaneo (Victor Buck Services) and Elantas, and show how we successfully tested their sustainable RFID design.
Screen-printing is an additive dry printing process where inks, or print pastes are used to create patterns on substrates through a fine mesh of threads. Nowadays, with the latest further developed conductive inks, screen printing enables to print RFID antenna structures on more economic and flexible substrates, such as cellulose-based and synthetic paper. In this presentation, we will explore upon the practical functionality of producing single layer ultra-high frequency (UHF) and multi-layer near-field communication (NFC) radio frequency identification (RFID) transponders that are screen printed on various flexible substrates. In focus will be the prerequisites and process principles, types of inks and substrates, key requirements, challenges and limitations. Additionally, we will discuss tag performance and quality assurance topics for some critical parameters, such as antenna resistance and chip assembly requirements, to illustrate the key requirements upon printing RFID antennas. The technology and processing lays a groundwork for an innovative, sustainable, scalable and economically competitive production of RF antennas for RFID and NFC applications and smart labels, Internet-of-Things (IoT) applications, on-body-sensor monitoring for bio medical and sports solutions.
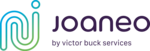
Luis Da Cunha Syaiful Mohd
Printed Electronics Supervisor RFID Field Engineer
Victor Buck Services Victor Buck Services
With this presentation we address the current trends occurring in the world of Human Machine Interface (HMIs). The presentation highlights the importance of the flexibility and innovation, additionally addressing challenges in the field. The presentation is supported by tangible examples of HMIs and functional labels. It provides an insight into the anticipated future trends and demands and challenges coming with them.
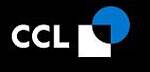
Maja Besednjak Robert Bromley
R&D Engineer Director Business Development
CCL Design Stuttgart GmbH CCL Design UK
Automated integration of (functional) foils to a particular device is often a very challenging task in the production process, especially when 3D geometries are involved. For this purpose the KURZ Group developed the patent-pending Functional Foil Bonding (FFB) process that is suitable for a high degree of automation. Especially, this post mold process is capable of bonding foils to surfaces that exhibit 3D geometries. In this presentation the basic principles of the FFB process are introduced. Advantages, possibilities, and limits of this approach, which allows integration of foils providing function and/or light to the device, are further discussed at the example of different current series projects.
In the presentation Kai & Sharif will show the advantages of screen printing versus other printing techniques.
The IMD/FIM process steps, from screen printing, high-pressure forming, UV curing, trimming and backmolding will be shown by means of functionalized automotive interior and exterior parts.
The requirements on the final automotive parts are getting tougher. Therefore, the adhesion in compound (ink / film / injection molding material) needs to be nearly undetachable and the surface hardness of film or first surface lacquer needs to be chemical and abrasion resistant.
The latest IMD/FIM automotive parts are functionalized, this means that the film insert molding technology is combined e.g. with a second functional film printed with conductive pastes.
We will show optimized ink layer constructions (one & two film) to protect the conductive pastes during injection molding and to improve cohesion in compound and long term stability of the final IMD/FIM+PE part.
Kai & Sharif will show a range of non-conductive color shades to prevent interaction and interference with the conductive pastes.